MD Robotics Custom Laptop Link Used by Astronauts to Visualize Shuttle Arm Position.
Astronauts on the Space Shuttle need to visualize the position of the robot arm used to service satellites and do other work in the cargo bay-without having to suit up and go for a space walk to look at it. When other vendors turned down the job, Sealevel designed a custom PC Card to interface the arm to the astronaut laptop in a very brief time. It has now flown successfully on multiple missions.
The Space Shuttle Remote Manipulator System
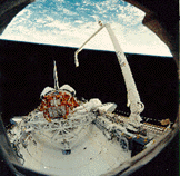
MacDonald Dettwiler Space and Advanced Robotics Ltd., operating as MD Robotics, has over 30 years experience in space robotics. Best known for the Space Shuttle Remote Manipulator System (SRMS) or Canadarm, MD Robotics developed and built the first Canadarm under contract to the National Research Council of Canada, as Canada's contribution to NASA's Space Shuttle program. Subsequently, NASA ordered four additional units to augment its fleet.
The SRMS consists of a shoulder, elbow and wrist joint separated by an upper and lower arm boom. The shoulder joint has two degrees of freedom, the elbow joint has one degree of freedom, and the wrist joint has up to three degrees of freedom. At a total weight of approximately 905 lbs., the Canadarm has recently been upgraded to maneuver payloads of up to 266,000 kgs. in the weightlessness of space. Canadarm uses an end effector with a specially designed grapple fixture to capture payloads and place them in orbit.
Challenge of Linking to the SRMS
Prior to working with Sealevel, the astronauts had to be able to see the robotic arm in order to operate it. The arm could become immobilized if the astronauts couldn't make direct visual contact.
The General Purpose Computer (GPC) aboard the Shuttle communicates with the Canadarm through the Manipulator Controller Interface Unit (MCIU). Integral to this communication link is a non-commercial protocol, which must be understood by the laptop connected to the MCIU. Another hurdle that had to be overcome by the design team was the lack of space. Typically, laptops have sufficient interfaces to accommodate two PC Cards. The laptop intended for connecting to the MCIU was no different; however, its two PC Card slots were already taken. The challenge then became not only designing a PC Card able to understand the language of the MCIU, but also designing one that included the functionality of the PC Card to be replaced. MD Robotics found no commercial PC Cards able to run the MCIU protocol, let alone PC Cards incorporating the additional functionality. A custom design was decided to be the appropriate solution.
Creating the 9009 Interface
Sealevel and MD Robotics worked together to design a multiport PC Card that could interface between the Payload and General Support Computer (PGSC) and the MCIU of the SRMS, and other serial asynchronous RS-422 communication devices. The multiple function PC Card system comprises the 9009 (a type II specification 2.1 compliant PC Card), interfacing cable, external cable, and Windows 95/98 Driver. The 9009 provides three independent communication channels: one serial synchronous data acquisition channel, and two serial asynchronous RS-422 channels.
The first spin on the board was completed in June 2000. This revealed the presence of a bug in the original specifications, so Sealevel respun the design in three weeks to compensate for the bug.
Proton irradiation tests were carried out in August 2000 and the card passed with a projected Mean Time Before Failure of greater than 10 years within the orbital altitude and inclination range of the Space Shuttle.
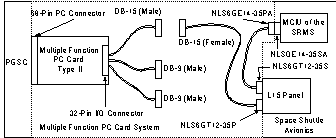
Results
The 9009 interface was first used on the Shuttle flight in October 2000 and has been used on each flight since then. In the photo on the first page, Canadian Astronaut Marc Garneau operates the Shuttle's Canadarm with the 9009 installed on his laptop.
Now-with the Sealevel board installed-astronauts aboard the Space Shuttle operate the robotic arm without physically seeing it. The astronaut operating the arm uses a laptop computer with Sealevel's board connected through a cable to the robotic arm. The laptop display enables the crew to see the movement of the arm through the eyes of a computer, not the eyes of a human. As the arm is moved, it sends data to the 9009 board, and then onto the graphic screen on the laptop. The graphic screen is instantly updated with a 3D picture of the arm's exact location.
Marius Pop, the MD Robotics engineer responsible for the design, is enthusiastic about results. Asked if he's happy about how the project turned out, he says, "It was only four or five months from design to board. How could you not be happy?" He adds, "In talking to the Sealevel design team, they would always have an explanation and a fix ready for any questions we had. They were very experienced, easy to talk to and always had the solutions." He notes that he chose Sealevel, "because they were ready to devote the resources to development of this, even though it's not likely to be stock product for them. Many small companies won't devote those resources to a project like this-in fact, another company we also approached just stopped returning our phone calls!"
|