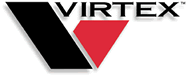 |
Virtex-E
Extended Memory Technical Backgrounder
|
|
Xilinx and UMC Deliver Copper in New FPGA Family
Collaboration Sets Stage For Higher Performance FPGAs
Over the past two years, Xilinx engineers have worked in close collaboration
with UMC towards the development of copper-based FPGAs. Today, Xilinx is
announcing the new Virtex-E Extended Memory FPGA family, the first programmable
logic available with copper interconnect. This is a major breakthrough
with long-term benefits for systems designers looking for maximum performance
with minimum power dissipation. This document provides some technical background
on UMC's damascene copper technology, its fabrication processes, and the
corresponding benefits seen within Xilinx' FPGAs.
The Natural Evolution to Copper
In order to meet ever-increasing bandwidth and density requirements,
FPGAs must utilize the latest technologies to achieve the highest possible
performance.
In today's leading-edge process technologies, the interconnect architecture
is the key limitation for IC performance. Copper interconnect, with its
superior resistivity and scalability over standard aluminum-based interconnect,
will allow higher device performance and quicker migration into 0.15 micron
and smaller geometries.
UMC and Xilinx have had a close technology partnership for many years,
resulting in a tradition of technology leadership including:
- First FPGA shipped in 0.25 micron technology
- First FPGA shipped in 0.18 micron technology
Continuing this tradition, UMC and Xilinx delivers the first available
FPGA employing leading-edge copper technology. The new VirtexTM-EM family
is manufactured in UMC's production fab, with the equipment and production
facilities in place for production ramp-up.
This is a very significant step for the semiconductor industry, as UMC
becomes the first dedicated foundry to ship product using copper technology.
UMC joins an elite number of leading companies such as IBM, Motorola, and
TI as among the first to have copper technology running in a production
fab. The joint development between Xilinx and UMC on this technology allows
Xilinx to ramp-up quickly on new high-performance FPGA families using copper
technology for 0.18 micron and smaller geometries.
UMC's Damascene Copper Technology
· Dual damascene copper interconnect
· Low-k dielectric
· Production fab
· Two layers moving to all layers
Damascene copper processing is fundamentally different from aluminum
processing. Copper is a softer metal than aluminum and is more difficult
to deposit chemically and to remove with chemical etches. Therefore, damascene
copper technology uses different steps and equipment than those used in
aluminum processing. In the current copper process, trenches are created
in the silicon dioxide insulator before the copper is applied. This is
opposite to aluminum, where the insulator is patterned after the aluminum
alloy is deposited. In the next step, inter-layer connections locations
(electrical "vias") are patterned as open holes that expose the underlying
metal layer at the bottom of certain trenches. A barrier metal is deposited
to the entire wafer surface that covers not only the top side of the wafer,
but also the trenches and the sides and bottom of the vias. Once the barrier
metal covers the entire wafer evenly, copper is electroplated on top to
the desired thickness.
The wafer then undergoes chemical-mechanical planarization (CMP), which
is analogous to a chemically enhanced mechanical grinding process that
levels the wafer. This step eliminates all copper and barrier metal except
those within the trenched locations. The result is patterned islands of
copper embedded within the insulator trenches, with an extremely flat surface
suitable for further metal layers. The insulator uses a proprietary low-k
dielectric material, which provides superior capacitance characteristics
over standard silicon dioxide.
The initial copper and low-k dielectric is used in the top two of the
six total layers of metal interconnect. This maximizes the benefits of
copper for high performance devices by reducing internal voltage drops
and clock skews while maintaining the mainstream aluminum capacity for
faster production ramp-up.
New Technology Solutions
· Copper CMP chemistry
· Metal pattern density
A key requirement for copper technology is the clean removal of extraneous
metal outside of the trenches without scratching the surface, which requires
optimization of chemical slurries. Optimizing the CMP process to clean
the surface without damaging the copper, one of the softest metals used
in semiconductor processing, was a major challenge. The process must guarantee
the uniformity of surface thickness of each layer. For example, large areas
of copper will suffer a tapering effect whereby the center will be thinner
than the edges. Xilinx and UMC engineers developed an algorithm for automatically
equalizing the metal density, by adding dummy patterns in sparse areas
and slotting large patches of metal.
Challenges of High Performance FPGAs
· Interconnect limitations
· Power dissipation
· Power distribution
· Electromigration
High-density field programmable gate arrays (FPGAs) have among the highest
number of transistors of any integrated circuit. With continuing demand
for faster time-to-market, shorter design cycles, and increasing logic
complexity, this trend is expected to continue into the next decade. These
complex FPGAs challenge process technologies to deliver increased transistor
density, higher performance, and lower power dissipation per logic gate.
To understand the effects of exponentially increasing density and performance,
consider the XCV2000ETM FPGA with over two million usable gates. These
devices are typically used in systems with clock frequencies over 250 MHz
and I/O speeds up to 622 Mbps. In such cases, the dynamic power dissipation
of a fully utilized chip operating at 1.8 volts may exceed 10 watts, depending
on the exact design and clock rates.
To support these types of designs, the internal chip is designed to
withstand power dissipation substantially in excess of 20 watts over an
operating lifetime in excess of 20 years. On-chip power distribution uses
primarily the top two metal, which have the greatest metal thickness resulting
in lower current density (i.e. amount of electrical current per cross-sectional
area. Electromigration is caused by the flow of electrons that tend to
push metal atoms out of the metal lattice, resulting in a gradual redistribution
of the metallic lattice. If current density limits are exceeded over an
extended period of time, the on-chip wiring can fail due to electromigration,
whereby the wire becomes distorted and eventually disconnected.
With FPGA densities doubling approximately every 18 months, along with
increasing internal clock frequencies, traditional process technologies
are challenged to keep pace. For example, an FPGA that is twice the size
of the XCV2000E device will have over 300 million transistors, with frequencies
in excess of 500 MHz and dynamic power dissipation in excess of 15 to 20
watts. To meet such requirements using traditional aluminum alloy metalization,
it would be necessary to either increase the power bus widths (which increasing
overall chip size) or increase metal thickness (which reduces on-chip speeds).
With both densities and performance increasing exponentially, the material
limitations of aluminum are putting further Moore's Law predictions at
risk.
Damascene Copper for High Performance FPGAs
· Reduce voltage drop
· Minimize clock and signal skew
The primary goal of the development effort between Xilinx and UMC was
to provide an interconnect technology that enabled higher system performance.
Two key areas that effect system speed degradation had to be addressed:
(1) internal power supply voltage drop, and (2) clock and signal skew
For large, complex chips with substantial on-chip activity, there can
be a significant difference between the external and internal power supplies.
For example, a large chip driven by a stable 1.8-volt external power supply
can operate at 1.6 volts or less internally, due to large operating currents
that causes internal voltage drops. The performance of the internal circuitry
can degrade by 15 percent or more if a 12 percent voltage reduction occurs.
While this effect cannot be eliminated entirely, a substantially lower
resistance power supply connection will minimize the performance degradation.
Clock and signal skew will also degrade system performance because of
the need for added timing margin to neutralize their effect. This skew
is caused by the relatively high resistance of the aluminum wiring compared
to the variable capacitive loading at the outer reaches of the clock net.
In a large chip, a key signal such as clock can experience on-chip skews
of 0.5 to 1 nanosecond, which can degrade system performance by 10 percent
for clock periods of 10 ns or less. The result is a localized RC delay
effect at each destination that causes the clock signal to arrive at different
nodes at different times. This effect can also be minimized with a lower
resistance interconnection. Advanced copper interconnect technology can
be used to replace aluminum alloy in the top two levels of metal to address
these problems.
Looking Ahead
· Damascene copper is the new standard
· All layer copper
The advent of damascene copper for advanced interconnect is a revolutionary
step, since the semiconductor industry that has used aluminum alloys since
the invention of the integrated circuit. Xilinx and UMC will continue to
develop processes that take advantage of copper for all metal interconnect
layers, further improving performance and reducing power dissipation.
Conclusion
The drive toward further integration is causing a profound shift in
interconnect technology. Copper is poised to take over the role of aluminum
alloys for complex, high-density integrated circuits. UMC and Xilinx have
jointly anticipated this need, and as a result of a two-year collaborative
effort, developed production capabilities for new high-density FPGA products.
This important milestone of being the first FPGA vendor to use production
damascene copper technology will be key for both UMC and Xilinx to continue
their respective leadership positions.
Figure 1: UMC/Xilinx Copper Interconnect Used in Production Fab.
Figure 2: Copper Processing Steps.
Figure 3: All-Layer Copper Interconnect.
to view the
PDF files below.
To view entire document in pdf format with above figures included, click
here.
|